News & Updates
Matex News
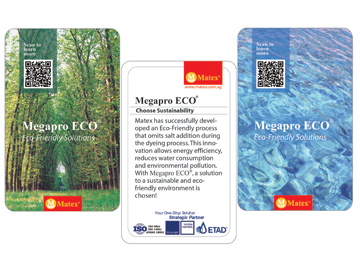
For the wet processing industry, the regulatory pressures continue to pile on. There are ever stricter enforcements of legislation on pollutant and effluent discharge and even harsher penalties for non-compliant behaviour!
In the recent article from ZDHC and Bangladesh PaCT, there is a call for a clearer breakdown of contaminants and chemicals discharge in textile wastewater. 50% and more is because of SALT!
There has been growing environmental awareness, the consumer too is now more cautious and demanding to have transparent and promoted environmental, social beneficial and economical viable sustainable solutions.
A recent article published 22th Oct 2018 from ECOTEXTILE reinforces this commitment to find and eradicate these hidden sources of hazardous textile pollutants.
There are for a long time many rules and regulations set up by Europe and USA which are playing an important role in driving sustainability across the textile supply chain.
CPSIA - Consumer Product Safety Improvement Act under US Legislation
IPPC - Integrated Pollution Prevention and Control - directive of European Union
REACH - Registration, Evaluation, Authorisation and Restriction of Chemicals (REACH) is a European Union regulation.
Step by OEKO-TEX - certification system for brands, retail companies and manufacturers from the textile chain who want to communicate their achievements regarding sustainable manufacturing processes to the public in a transparent, credible and clear manner.
GOTS - Global Organic Textile Standards - ensure the organic status of textiles from the raw materials through environmentally and socially responsible manufacturing all the way to labelling in order to provide credible assurance to the consumer.
Bluesign system - a solution to promote sustainable textile production. It aims to eliminate the use of hazardous substances right from the beginning of the manufacturing process.
Cradle to Cradle - Innovation Institute, a non-profit organization, administers the Cradle to Cradle Certified™ Product Standard
ETAD - organization representing the dye and pigment industries to minimise the adverse impact of organic colorants on health and the environment.
ZDHC Foundation – ZDHC and its roadmaptozero. A non-governmental environmental organization mainly focusing on areas like MRSL (Manufacturing Restricted Substances List) & Conformance Guidance, Wastewater Quality, Audit Protocol and Research.
Just to name a few, the textile wet processing industry and the dye/chemical manufacturers continue to fight and overcome immense key challenges!
And there is a cost associated with it -
Dye/Chemical manufacturers continue to invest heavily to innovate to remain economically viable by introducing new products which are - environmentally and economically sustainable, are able to increase productivity with less use of resources i.e. water savings of up to 50% and more, Energy savings of up to 50% or more, Time savings of up to 25% and more. These new products are sustainable but, since there is an additional cost associated with it, the Dye/Chemical manufacturers hope or rather expect that the industry can share part of these related expenses.
The industry on the other hand is eager to adapt the sustainable solutions however, when they realise that it will have affect their competitiveness in a cut throat business environment as well as dip into their profit margins, they become hesitant and prefer often to continue with the traditional/conventional methods.
There is immense and intense competition in Fashion and Apparel Industry/brands for new products in shorter time intervals with more attractive designs, better performance, better quality, lower prices, and instant availability.
Can Lower prices & Sustainability thus really walk together?
Are consumers like you, me and the Fashion/Apparel Industry/brands willing to incorporate sustainable cost while we source for better products? More recognition should be given to those industry players who continue to demonstrate competence and a serious commitment to the sustainability agenda.
The brands could use a differentiating price strategy to establish its product as a high-quality product in the minds of consumers and encourage industry players to adapt a common goal of sustainability.
Matex International Limited, a Singapore listed specialty chemical producer has since launched its latest next generation process solution Megapro ECO® for clean colour science technologies.
Megapro ECO® enables the dyeing of cotton without the need for salt additions.
We at Matex, care immensely for our environment and are dedicated to assisting brands, retailers and industry partners to implement sustainable textile production that meet quality and eco-requirements making efficient use of our limited resources.
Matex as a ETAD Member and bluesign® System Partner is committed to the Zero Discharge of Hazardous Chemicals (ZDHC) to define and continue to work out Manufacturing Restricted Substances List (MRSL) for the apparel and footwear industry.
This latest innovation builds on its poly functional dyestuff range "Megafix® RE" cotton/reactive which enables fabric and garment dyers to conduct low temp 40 degree dyeing. This range similarly targeted Energy Saving and Eco Friendly conscious customers.
Megapro ECO® uses EXISTING dyeing equipment and it significantly helps to reduce water, energy and time related cost. Importantly with the aim to meet ever stringent environmental regulations like TDS (total dissolved solids), COD (chemical oxygen demand), BOD (biological oxygen demand) and color requirement levels from the wastewater effluent in accordance to ZDHC guidelines, enabling easier treatment and reducing overall effluent cost.
Other benefits of adopting a no salt process can include but not limited to savings –
- on buying truck-loads/transportation of salt.
- for loading/unloading i.e. labour cost related to salt.
- on storage spaces, which can be best utilised for other better economic returns.
- a Modern Plant Setup.